Zero-Strength Time of PCTFE in Aerospace
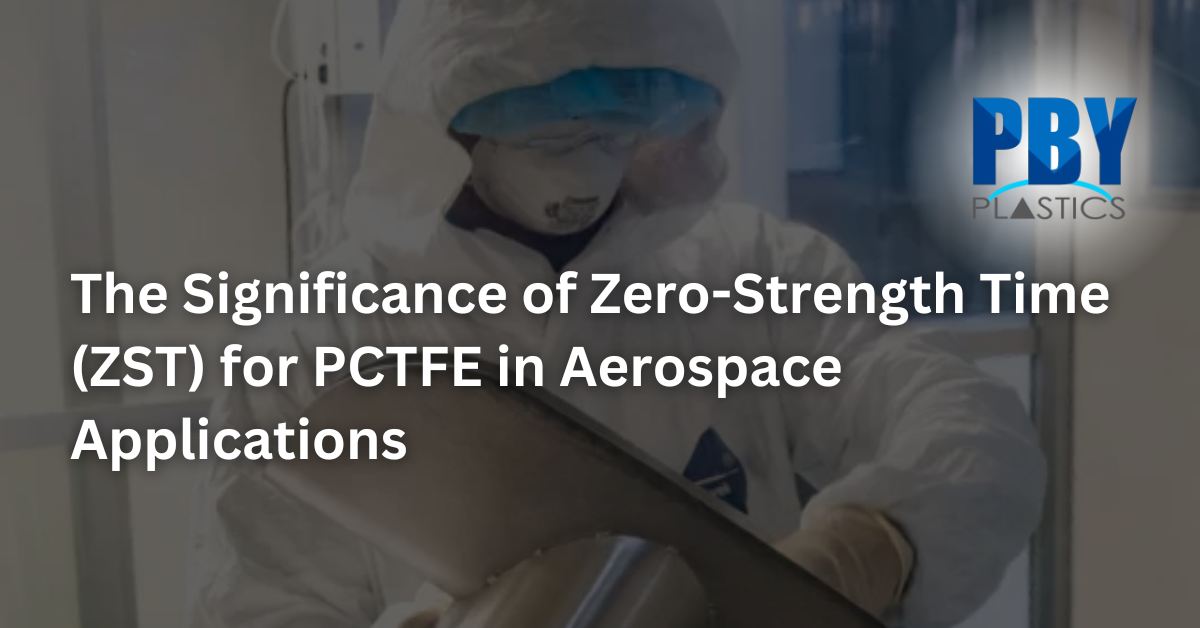
In aerospace engineering, material selection plays an important role in ensuring the safety and performance of aircraft and spacecraft. Polychlorotrifluoroethylene (PCTFE) has become a key player. One of the tests to assess the viability of PCTFE in aerospace applications is zero-strength time (ZST).
ZST is also significant in the development and refinement of PCTFE formulations. By understanding the conditions that lead to the loss of mechanical integrity, chemists and material scientists can enhance the material's properties, such as its resistance to cracking under pressure and its overall strength.
Understanding Zero-Strength Time
Zero-strength time measures the time it takes for a material sample (such as PCTFE) to fail or break under a predetermined load and temperature. The results from ZST reveal the material's molecular weight and structural integrity, which directly relate to its mechanical properties and overall performance. For aerospace applications (where materials are subjected to extreme conditions), ZST ensures that PCTFE components can withstand the rigors of their intended use.
PCTFE: A Game-Changer in Aerospace Engineering
Polychlorotrifluoroethylene (previously known as Kel F and now as NEOFLON™) has high chemical resistance, thermal stability, and mechanical strength, making it ideal for aerospace applications. Its low-loss dielectric properties and radiation resistance make PCTFE valuable for electrical systems within aerospace vehicles. Using glass reinforcement enhances its wear resistance and suitability for bearing applications in challenging environments.
Ensuring Quality with Standards
Several standards govern the use of ZST and PCTFE in aerospace applications to guarantee compliance and quality control:
- ASTM D1430: Provides a classification system for PCTFE polymers, establishing essential properties and application guidelines.
- AMS 3645, AMS 3646, and AMS 3650: Define the requirements for different PCTFE grades and basic semi-finished shapes as a function of the processing method.
- ASTM D7194: Focuses on finished parts machined from PCTFE for aerospace applications.
The Vital Role of Zero-Strength Time (ZST) in Aerospace Components
In aerospace engineering, ZST is a critical tool for evaluating PCTFE's mechanical strength and durability. The findings enable engineers to make informed decisions regarding PCTFE's utilization in aerospace components like seals, gaskets, valves, pumps, and tubing. Compliance with stringent standards ensures PCTFE maintains its structural integrity and performance under extreme conditions.
The application of ZST in evaluating PCTFE also enhances the safety protocols of aerospace vehicles. Engineers use ZST to pinpoint failure points and enhance component safety.
Elevating Aerospace Standards with Zero-Strength Time (ZST)
Zero-Strength Time is a fundamental evaluation method for assessing the suitability of PCTFE in aerospace applications. By providing data on PCTFE's material properties, ZST improves safety and efficiency in aerospace technologies. As aerospace engineering progresses, the use of ZST and compliance with established standards will continue to be essential for the development of safer and more reliable aerospace solutions.
ZST also fuels innovation within aerospace material science. Through testing and analysis, researchers and engineers can explore new ways to optimize the properties of PCTFE for even more demanding aerospace environments. This ensures aerospace technologies meet current regulatory and performance standards and will likely exceed the expectations of future aerospace missions, securing a safer and more efficient path forward.
For inquiries regarding PBY’s zero-strength time capabilities and advanced aerospace solutions, contact us.