PCTFE vs PTFE: Material Comparison
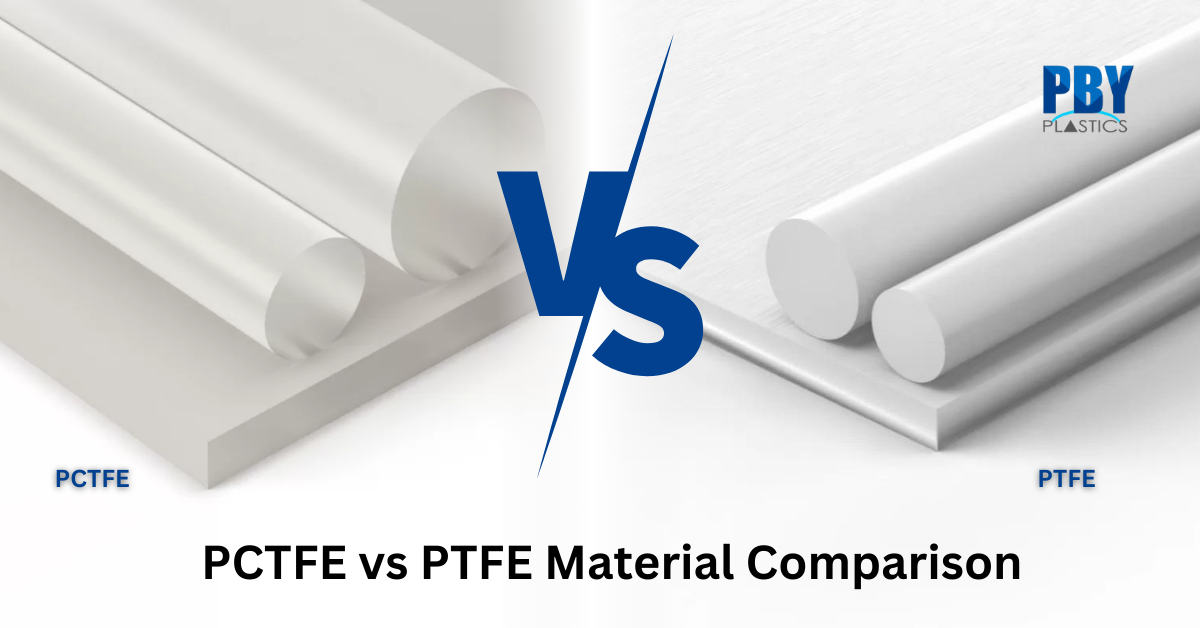
When working with polymer materials, understanding the nuances between similar substances is key to ensuring you select the right material for a specific application. Two such materials are PCTFE (polychlorotrifluoroethylene) and PTFE (polytetrafluoroethylene). Each has distinct advantages for different uses.
Chemical Structure
PCTFE and PTFE share the same fluoropolymer base, but they differ in their chemical structures, which gives them their distinct properties.
The chemical structure of PCTFE
PCTFE (also known by its trade name Kel-F®) has a chlorine atom in place of one of the fluorine atoms. The substitution of chlorine for fluorine results in increased rigidity, reduced permeability, and improved dimensional stability.
Illustrative drawing of PCTFE structure
The chemical structure of PTFE
PTFE (more commonly known as the brand Teflon®) is composed of carbon and fluorine atoms, resulting in a fully-fluorinated compound. The all-fluorine environment around the carbon chain provides PTFE with its properties of high chemical resistance, low friction, and high thermal stability.
Illustrative drawing of PTFE structure
Properties
The properties of PCTFE and PTFE give the materials the characteristics that make them suitable for a variety of different environments and applications.
Temperature Range
PCTFE has a typical service temperature range of -255°C to 180°C (-427°F to 356°F). This makes the material suitable for cryogenic applications. Industries such as aerospace and refrigeration use PCTFE in their systems.
PTFE has a temperature range of around -260°C to 260°C (-436°F to 500°F). This makes it suitable for use in environments that experience both extreme cold and high heat. Its thermal stability is key in applications like high-temperature seals, gaskets, and linings in the chemical processing and semiconductor industries.
Mechanical Strength
PCTFE has higher mechanical strength, rigidity, and dimensional stability than PTFE, especially at lower temperatures. This makes it particularly useful in applications that require tight tolerances and less deformation under load, such as in precision components and cryogenic valves. Its low moisture absorption and minimal gas permeability also contribute to its mechanical robustness.
Although PTFE is slightly less rigid and mechanically robust, it offers low friction and high conformability. This makes it suitable for applications where sliding movement is critical, such as in bearings, bushings, and nonstick surfaces. Its adaptability under load enables PTFE to conform to irregular surfaces, which enhances its sealing capabilities.
Chemical Resistance
PCTFE also has excellent chemical resistance, although slightly less than PTFE, particularly at high temperatures. It is resistant to chlorine and hydrochloric acid, which makes it useful in applications involving these chemicals, such as in the production of chlorine gas.
PTFE is highly inert, resisting almost all chemicals, with the exception of some molten alkali metals and fluorine at high temperatures and pressures. This makes PTFE the material of choice for containers and pipelines handling highly-corrosive substances in the chemical industry as well as for linings in nuclear reactors and spacecraft.
Electrical Insulation
Both polymers offer excellent electrical insulation. However, PTFE outperforms PCTFE due to its wider temperature range, which ensures it has consistent insulation under extreme conditions. Its dielectric strength remains stable across various frequencies, making it suitable for high-frequency electronics, coaxial cables, and connector assemblies.
PCTFE also provides reliable electrical insulation. Its low dielectric constant and dissipation factor make it ideal for applications requiring stable and high-performance insulation, such as in capacitors and high-voltage insulators.
Radiation Resistance
PCTFE exhibits greater resistance to radiation compared to PTFE, making it an excellent choice for aerospace and outdoor applications where exposure to radiation is a concern. Its ability to maintain structural integrity and resist degradation under prolonged radiation makes PCTFE the preferred material for satellite components, outdoor electrical insulators, and greenhouse coverings. In contrast, PTFE is more prone to degradation under radiation, making it less suitable for environments where radiation resistance is essential.
Transparency
PCTFE can be one of the most transparent fluoropolymers available. Transparency is related to the crystallinity of the polymer and can be controlled during processing. This characteristic makes it ideal for applications where visual transparency is a necessity, such as in sight glasses for chemical processes, protective covers, and components within optical instruments.
As PTFE is typically opaque, it is utilized in applications where optical clarity is not essential.
Applications
PCTFE is often used in applications requiring long-term exposure to harsh climates, such as in cryogenics and aerospace, due to its UV transparency and low moisture absorption. The material's high mechanical strength and stability at low temperatures give it an important role in the manufacturing of cryogenic valves, seals, and gaskets. Additionally, its resistance to chlorinated and halogenated chemicals makes it the preferred choice for components in chemical processing plants and laboratory equipment. It is also used in the pharmaceutical industry — in the production of blister packaging to protect sensitive medications from moisture and contamination.
PTFE is used in applications that require extreme chemical resistance or need to withstand high temperatures, such as industrial gaskets, coatings, and linings. In the medical field, PTFE is widely used for its biocompatibility and low friction, which make it ideal for catheters, surgical instruments, and grafts. In the semiconductor industry, PTFE is chosen for excellent dielectric properties in the fabrication of high-frequency electronics and insulating components.In aerospace, PTFE is often chosen for insulation for wiring and cables in aircraft due to its stability across a wide temperature range and resistance to harsh environmental conditions.
Pros and Cons
When comparing PCTFE to PTFE, neither is inherently better — rather, it depends on the application. PCTFE has a higher mechanical strength and transparency, but the material is more expensive and has a lower temperature range. PCTFE's low outgassing makes it suitable for vacuum applications.
PTFE has high temperature and chemical resistance, but it is less mechanically robust and lacks the transparency of PCTFE. Although it is nonstick and has low coefficient friction (which is useful in many industrial applications), its lower mechanical strength may necessitate structural support or reinforcement in certain uses. Furthermore, it is important to consider PTFE’s tendency to creep under mechanical stress (particularly at higher temperatures) when designing components that will be subjected to prolonged loading.
Understanding these characteristics will allow engineers and designers to select the most appropriate material for their operational needs and the environmental conditions. This will optimize the performance and longevity of the final product.
Conclusion
Both PCTFE and PTFE are widely used, but the right material depends on the application. Understanding the distinct properties of the two materials is crucial for improving product durability, safety, and efficiency. It is essential to consider factors such as environmental conditions, mechanical stress, chemical exposure, and budget.
Ongoing advancements in polymer science continue to improve the characteristics of both PCTFE and PTFE, expanding their potential applications and enhancing their responses to new industrial challenges.
Our experts can provide you with further assistance in selecting the right fluoropolymer for your application. Contact us for personalized support to make the best choice for your project.